(报告出品方/作者:华创证券,范益民)
一、强弱之论:日本和美国工业机器人的发展差异
(一)美国:工业机器人诞生地,成本过高+政府引导不足
世界上第一台工业机器人在美诞生。1956 年美国发明家乔治·德沃尔(George Devol) 和物理学家约瑟·英格柏格(Joe Engelberger)成立了一家名为 Unimation 的公司,并于 1959 年推出了世界上第一台工业机器人,命名为 Unimate。1961 年,Unimation 公司生 产的世界上第一台工业机器人 Unimate 在美国通用汽车公司安装运行。这台工业机器人 用于生产汽车的门、车窗把柄、换档旋钮、灯具固定架,以及汽车内部的其他硬件等。 遵照磁鼓上的程序指令,Unimate 机器人 4000 磅重的手臂可以按次序堆叠热压铸金属件。 Unimate 机器人成本耗资 65000 美元,但售价仅为 18000 美元。
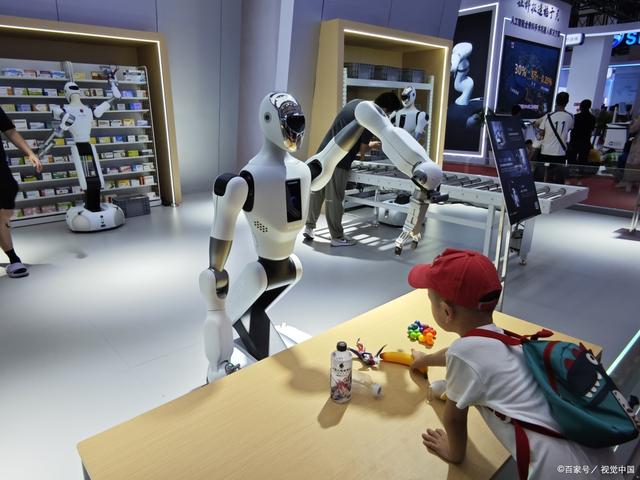
1960 年代工业机器人每小时成本高达 5.5 美元左右。我们参考当时 Unimate 的制造成本 做出如下假设: 1)安装调试费用约为工业机器人本体价格的 5%,每年检测维修和升级改造费用约占工 业机器人本体价格的 15%; 2)当时每台工业机器人使用寿命约为三年,除去节假日每年 50 周;检测维修和升级改 造时间占使用时间 30%; 3)工业机器人每小时成本费用=(本体价格+其他所有费用)/工作时间。 经过测算可以得出 1960 年代工业机器人每小时成本费用约为 5.53 美元。
相比于当时美国制造业平均时薪,工业机器人使用成本过高。工业机器人的初始投资成 本较大,包括购买机器人本体、安装调试费用以及维护和修理费用,尤其是在技术还不 够成熟、维修服务不够普及的情况下。1960 年,美国制造业人员平均时薪仅为 2.1 美元 左右,直到 1977 年前后才达到工业机器人的使用成本,极大限制了企业尤其是制造业 公司采用工业机器人技术的能力,巨大的成本差异使得企业需要权衡投资回报率和长期 效益之间的关系。
1960 年代美国制造业劳动力充足,失业率维持高位,无需工业机器人大批量应用。第 二次世界大战后,美国迎来生育高峰,导致 60 至 70 年代劳动力充沛。根据美国劳工部 统计,60至 70年代美国制造业就业人数达到历史高位,介于 1200万至 1500万人之间, 充足的劳动力资源使得“机器替人”的迫切性较低。同时,从 60 年代末开始,美国失 业率攀升,从 4%上升至约 10%。当时,美国政府的主要任务是提供更多就业岗位以降低失业率,而不是发展工业机器人以避免更多人失业。因此,政府既未将工业机器人列 为重点发展项目,也未给予财政支持或组织科研力量加强研发。
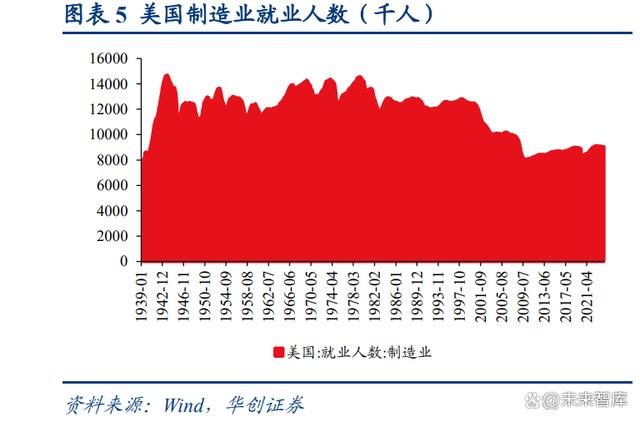
工业机器人的成长与当时美国就业政策存在冲突。美国政府的政策指引方向是积极创造 就业机会,提供职业培训和教育项目,以增强工人的技能和就业竞争力。此外,政府高 度重视工人权益,实施了多项促进就业的措施,如失业救济、就业援助和工会支持。这 些政策在很大程度上缓解了失业问题,但也间接阻碍了机器人技术的普及。工业机器人 作为劳动力的替代品,其推广会减少工业企业对于劳动力的需求,进一步加剧失业状况的发生。这种政策环境使得美国工业机器人的发展步伐相对缓慢,形成了技术进步与就 业保护之间的矛盾和冲突。
美国制造业企业盈利能力持续处于低位,整体对工业机器人等设备资本开支意愿较弱。 企业的盈利能力和对新技术、新设备的资本开支呈强正相关。由于利润不足,许多美国 制造业企业难以承担工业机器人高昂的初期投资和维护成本,进一步限制了工业机器人 的广泛应用。据美国经济分析局,1960 到 1970 年代,美国制造业企业利润维持在 300 亿美元以下,设备投资额在 200 亿美元以下,处于相对较低水平;受制于经济压力和盈 利能力下降,制造业企业更倾向于控制成本而非大规模投资于自动化设备,延缓了工业 机器人在美国的普及和发展。
国内需求低迷叠加政府支持力度较小,美国本土工业机器人制造商面临产量、盈利双重 困境。据 1983 年美国国际贸易委员会发布的《COMPETITIVE POSITION OF U.S. PRODUCERS OF ROBOTICS IN DOMESTIC AND WORLD MARKETS》分析了 1979 至 1982 年间美国工业机器人产业的发展情况。自 1961 年第一台工业机器人问世以来,到 1979 年美国国内的工业机器人产量仅为 614 台,产能利用率约为 50%。美国工业机器人 制造商普遍出现亏损现象。美国工业机器人制造商盈利的中位数在1979年为亏损23%, 而 1983 年更是达到了亏损 49%。在这种形势下,美国企业选择进行技术输出,开拓海 外市场,以应对国内市场的萎靡和高额亏损。然而,这一策略也导致美国错过了工业机 器人快速发展的关键时期。
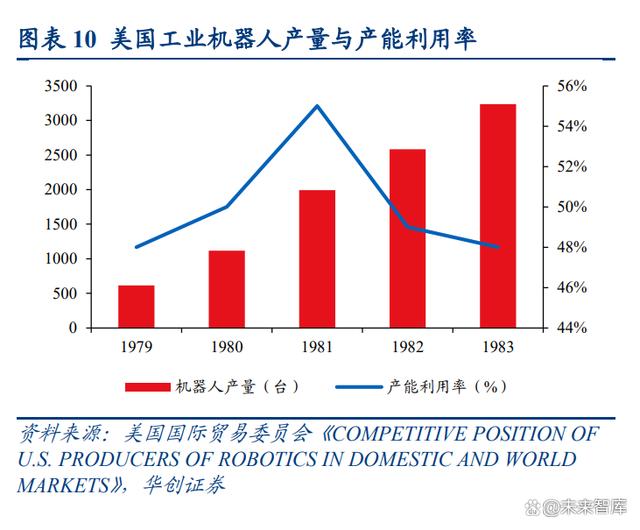
(二)日本:工业机器人的发扬地,劳动力短缺背景下,下游需求的爆发
日本成为“工业机器人王国”,在国际市场占有重要份额。日本自 1960 年引入工业机器 人概念后,开始了自主研发和生产机器人的道路。日本在 1967 年由川崎重工业公司从 美国 Unimation 公司引进机器人及其技术,1968 年试制出第一台川崎的“尤尼曼特”机 器人。80 年代中期,日本机器人的产量和安装的台数在国际上跃居首位。经过几十年的 发展,日本在工业机器人领域培养了非常强大的实力和影响力。工业机器人龙头如发那 科(FANUC)、安川(Yaskawa)、川崎(Kawasaki)等在全球范围内享有很高的地位。
日本工业机器人拥有雄厚的技术实力和完善的产业链。日本工业机器人产业链涵盖从核 心零部件制造到整机集成和应用的各个环节。日本企业如哈默纳科、纳博特斯克在上游 零部件领域处于领先地位,中游整机厂发那科、安川支撑了工业机器人的高精度和高效 率,下游日产汽车等则为最好的应用场景。强大的供应链管理与上下游企业的密切合作, 确保了日本工业机器人产业在技术创新、质量控制和市场响应方面保持世界领先水平。
日本工业机器人发展史大致可分为四个阶段,迅速完成产业链布局。20 世纪 70 年代, 日本劳动人口比例下降,劳动力成本上升,同时日本汽车行业崛起对汽车生产自动化需 求旺盛,在这样的背景下,日本工业机器人行业迎来 30 年左右的黄金发展期。日本工 业机器人发展史可分为“摇篮期”、“实用期”、“普及提高期”和“平稳增长期”,其中 1980 年起工业机器人的大规模应用缓解了日本劳动力不足的问题,同时帮助提升了制造 业的生产效率,实现了工业机器人行业跨越式的转型与升级。
20 世纪 60-80 年代,日本经济全面增长,对于劳动力的需求显著增长。据建行投行公众 号援引日本内阁府和日本财务省的数据,日本 GDP 由 1960 年的 160097 亿日元增长至1980 年的 2428387 亿日元,期间 CAGR 为 14.56%;快速增长的背后离不开日本工业的 支撑和发展,同时期工业增加值占 GDP 比重维持在 37%-43%。然而,尽管日本经济和 制造业的迅猛发展带来了对劳动力的大量需求,但劳动力供给却未能跟上这一步伐。 1960年到1980年,日本制造业的雇员人数从333.69万人增长至811.24万人,期间CAGR 仅为 4.54%,远远低于经济增长的速度。劳动力短缺却导致了工资的快速上涨,从 1960 年到 1980年,制造业雇员的月均工资从 2.81万日元上升至 26.54万日元,期间 CAGR达 到 11.88%。为了应对劳动力短缺和成本上涨的压力,日本加快了工业机器人的引进。 1980 年,日本工业机器人的总产值为 784 亿日元,年产量达 19900 台;根据估算,当时 的平均每台工业机器人售价约为 393.97 万日元,这一价格与一名制造业雇员一年的工资 相差无几,工业机器人逐渐成为替代劳动力的重要手段。
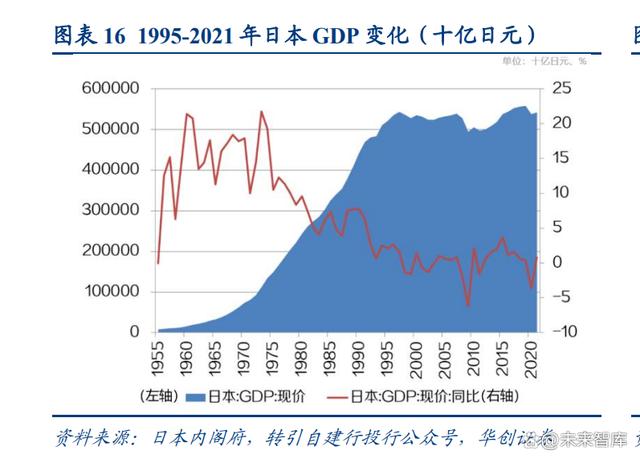
社会老龄化加剧,制造业劳动人口短缺现象较为明显。在二战结束后,日本劳动力人口 短缺,推行鼓励生育的政策。然而,随着战后经济恢复和发展,日本仍然面临着劳动力 的缺口。据日本统计局数据,1980年以后,日本青少年和老年人比例基本维持在 30%以 上,到 2020 年达到近 40%;同时据世界银行数据,日本老年人的抚养比持续增长,从 1980 年的 13.75%提升至 2023 年的 51.43%,日本的劳动力市场面临着巨大挑战,尤其是 在制造业领域。制造业是劳动密集型行业,对劳动力的需求量大,对技能和效率的要求 也较高。随着日本经济的快速增长,制造业的规模扩大,对劳动力的需求也随之增加。 经济增长带来的需求增长速度可能超过了劳动力供给的增长速度。
日本失业率常年保持相对低位,充分就业状态为工业机器人发展创造良机。从失业率的 角度分析,20 世纪 60-70 年代,日本失业率不到 2%,属于充分就业状态。当产业规模 继续发展壮大,在效率不变的情况下,现有劳动力将出现不足。当劳动力需求远超劳动 力供给的增加,制造业企业面临缺工的问题。劳动力市场的僵化和劳动力流动性的限制 也可能阻碍了劳动力的有效配置。面临劳动力短缺的问题,许多日本企业开始采取多种 应对策略,包括提高工资和福利以吸引更多劳动者、改善工作环境以提高员工留存率、 引入自动化和机器人技术以减少对人力的依赖等。
下游汽车行业高速成长,对日本工业机器人行业发展起到关键作用。据建行投行公众号 援引日本自动车工业协会的数据,汽车制造业是最早采用工业机器人的行业之一,也是 机器人技术密集应用的核心领域。日本的汽车产业始于 1945 年,经过初期的积累,到 了 20 世纪 60 年代中期进入了快速扩张期。1960 年到 1967 年,日本的汽车年产量从 48.16 万辆猛增至 314.65 万辆。此外,日本的小排量汽车开始受到国际市场的青睐。 1976 年,日本汽车中超过 250 万辆用于出口;到 1980 年,这一数字攀升至 1104.29 万 辆,使日本成为全球汽车生产的领头羊。同时,汽车制造过程中,如焊接、喷漆等复杂 或危险的工序,应用工业机器人去代替人类从事高风险或重复性工作,提升了生产效率 和产品品质。同时,汽车制造企业资金实力雄厚,加速了工业机器人在汽车生产中的普 及应用。
政策大力扶持,助力日本工业机器人快速普及。日本政府在工业机器人产业实用期出台 多项政策扶持产业发展,在鼓励工业机器人生产企业研发创新的同时,持续减轻下游企 业使用工业机器人的成本,助力加快工业机器人普及。这些政策旨在通过建立行业标准 和分类制度来普及和促进工业机器人的应用,同时提供金融支持,包括融资租赁和贷款 制度,以降低企业采用新技术的门槛。此外,政府还通过税收减免政策减轻了企业的财 务负担,激励企业投资于技术创新。为了进一步加速技术进步和产业升级,日本还实施 了项目补助政策,支持工业机器人领域的研究与开发。日本成功地将其工业机器人行业 推向了一个新的高度,为国家的经济增长和技术进步奠定了坚实的基础。
通过对美国、日本工业机器人发展的分析可以看出,工业机器人发展离不开三个要素: 1)劳动力短缺是工业机器人产业发展的核心推动力; 2)发展强劲的下游应用领域是工业机器人发展的加速剂; 3)政府政策引导与支持是工业机器人发展的强力后盾。
二、得失之论:从财务角度出发,探寻发那科成功背后的内力和外力
(一)发那科:富士山下的“黄色”工业自动化传奇
发那科(FANUC)成立于 1972 年,前身是日本富士通公司专门负责自动化业务的部门 “富士通数控”,自创始人稻叶清右卫门博士 1956 年率先提出数控概念,公司一直处于 全球制造业革命的前沿。20 世纪 70 年代、80 年代,随着数控机床和工业机器人等世界 一流产品的出现,FANUC 战略从零部件向解决方案供应商拓展。2023 年 8 月,发那科 达成累计交付 100 万台工业机器人,这一数字再次刷新了工业机器人单一品牌的交付量 记录,是全球当之无愧的工厂自动化传奇。
以数控系统业务起家,进而延伸工业机器人、数控机床的产品布局。发那科拥有 FA (工厂自动化)、ROBOT(工业机器人)、ROBOMACHINE(数控机床)、SERVICE (服务)四大板块产品线。FA 产品线涵盖了数控系统(CNC)、伺服系统、激光器等基 础技术产品。ROBOT 产品线包括了不同功能和规格的工业机器人,如大中小负载协作、 弧焊、喷涂等等;同时配套应用场景,延伸两大核心零部件视觉系统和力传感器。 ROBO-MACHINE 是结合了数控系统和机械加工技术的复合型设备,如 ROBODRILL (小型加工中心)、ROBOSHOT(电动注塑机)和 ROBOCUT(线切割机)。SERVICE 主要通过 IOT 技术将 FANUC 的各种产品连接到网络中,实现数据的收集、分析和远程 监控,使得产品可以更加智能,提供预测性维护、能效优化和生产流程的实时测控等功 能。
FANUC 产品线之间形成互补和集成。FA 是基础,为工业机器人和数控机床提供必要的 控制技术和零部件。工业机器人和数控机床是 FA 技术的应用延伸,直接服务于工业生 产。IOT 则作为一种通讯交互方式,将 FANUC 的所有产品线连接起来,提升整个生产 系统的智能化水平,实现更高效的生产管理和决策支持。通过这种集成的产品线战略, FANUC 能够为客户提供从单一机器到整个工厂自动化解决方案的全方位服务,满足不 同行业和客户的定制化需求。
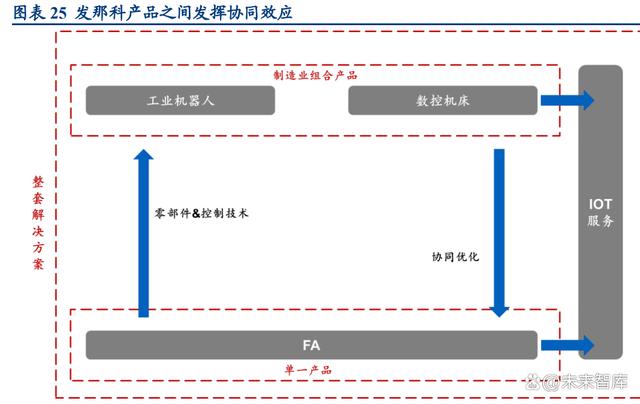
(二)营收端:看业务转型和时代背景
发那科创造了多项日本、世界的第一台产品。1956年,公司成功开发了日本首个私营部 门的数控系统(NC),实现了对机床的自动化控制,这在当时是一项革命性的技术突破。 1959 年公司开发了电液脉冲马达,1960 年第一台开环数控系统 FANUC 220 问世,1965 年首次开发出线切割数控系统,1966 年开发出第一台全 IC 型数控系统,1968 年全球首 个商业化 DNC 建成,1969 开发出全模块化 NC;这些创造历史性的产品为公司 NC 业务 确立了强大的市场地位。
二十世纪 70 到 90 年代,发那科数控系统业务创收压力增长。根据 Masato ITOHISA 《Fanuc’s Competitive Advantage and the Revolt of Machine Tool Builders: A Look at Fanuc’s User and Its User’s Customer Relationships From a Historical Perspective (1950s–1980s)》,发 那科在日本数控系统的市占率震荡下跌,从1972年的高位80.7%下降至1986年的50%; 全球制造业对自动化需求的增加,使得越来越多的公司进入数控系统领域,市场竞争愈 发激烈。这一时期,发那科不仅面临国内同行的激烈竞争,如三菱、安川等企业,也需 要应对国际市场上的挑战。激烈的竞争环境虽然推动了日本在全球数控系统的霸主地位, 同时也使得发那科营收增长存在压力。
二十世纪 90 年代到二十一世纪初,工业机器人、数控机床逐步起量。1974 日本首批工 业机器人、伺服电机顺利开发、安装并在 FANUC 工厂中应用。1985 年前后,日本数控 系统景气度下降,公司基于原始技术积累和下游需求的转变,拓宽工业机器人和数控机 床业务。日本车企自 1980 年初露头角,众多知名品牌丰田、本田日产在全球范围内的 影响力进一步提升,爆发式的需求增长与日本当时社会的劳动力短缺问题形成矛盾,为 发那科的工业机器人业务提供了广阔的市场;同时强大的数控系统实力让发那科的工业 机器人在精度上处于领先地位,从此发那科的工业机器人开始放量增长。
近 20 年,发那科整体营收、利润呈周期性波动。世界机床行业按照其使用寿命呈现 10 年左右为一个周期的特点,上一轮周期从 2009年开始,2011年到达顶峰后在 15-16 年经 历了迅速的回落;新一轮周期从 2019 年开始,整体仍为向上趋势。2014 至 2016 年间, 发那科的收入下滑,主要由于数控系统和数控机床销量的减少。2018 至 2019 年,受中 美贸易摩擦的冲击,发那科在中国的数控系统销售大幅下降,进一步影响了整体收入。 2023 年,发那科再次面临收入下滑的困境,主要归因于中国市场设备需求放缓,特别是 其核心业务工厂自动化部门复苏乏力,导致订单减少、库存增加。
(三)盈利端:看产品力和研发能力
发那科的毛利率、净利率相比于其他四大家族、国内工业机器人厂商保持绝对优势。四 大家族对比来看,发那科的毛利率虽有下滑趋势,但基本均维持在 35%以上,中枢值稳 居四大家族首位。同时发那科拥有在制造业中相当统治力的高净利率,稳定在 20%左右, 相比于 ABB、KUKA、安川,优势更加明显。与国内厂商对比来看,汇川的毛、净利率 与发那科相似,但两家厂商业务结构有所差异;相比于业务重合度更高的埃斯顿、埃夫 特,发那科的盈利能力遥遥领先。
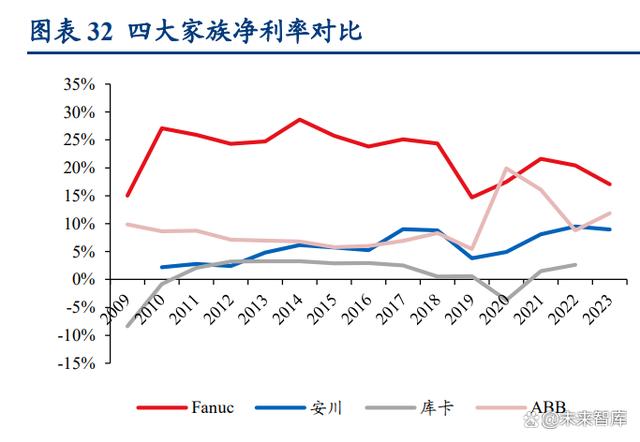
发那科的工业机器人核心零部件自供,实现产业链一体化。工业机器人产业链一般可以 划分为核心零部件生产、机器人本体制造、系统集成以及行业应用四大环节。核心零部 件中,减速机、交流伺服电机、控制器、驱动器则构成工业机器人的最核心部分。一般 而言,工业机器人产品同质化较为严重,厂家覆盖的产业链越长,对其掌控能力越强, 竞争力也越有望增强。通过延伸产业链,企业可以更有效地控制生产成本、提升产品质 量,从而在激烈的市场竞争中脱颖而出,取得更大的优势。发那科在伺服系统及控制系 统能够实现产品的自给自足,同时凭借其在数控机床领域多年的深耕,机床业务所带来 的零部件协同供应实现总体经营上的规模效应。发那科通过部分核心部件的自制以及在 系统集成业务上的协同效应,牢牢地锁住了工业机器人产业链上的大部分利润。
发那科拥有庞大的工业机器人体系,产品种类非常齐全。发那科工业机器人之所以能够 满足从轻型到重型的多种工业应用需求,是因为其拥有多达 240 种机器人产品系列,覆 盖了从 0.5公斤到 2.3吨的广泛负载能力,使得无论是精细操作还是重型搬运,都能找到 合适的机器人解决方案。这些机器人设计考虑了多样化的工作环境和条件,能够适应不 同温度、湿度和灰尘等环境因素,同时具备高可靠性和生产效率,通过故障诊断功能提 前预警潜在问题,减少停机时间。发那科还注重技术创新,如学习控制技术和内置视觉 功能,提高了动作的平稳性和速度,以及精准的定位和操作。 在不同的工业领域中,FANUC 的工业机器人能够提供多样化的应用场景,主要包括机 械加工行业、电子电气行业、食品饮料行业。在机械加工行业中,FANUC 机器人的应 用包括自动化上下料,这有助于提高生产效率,减少人工干预,同时降低劳动强度。它 们还负责精密装配,确保部件装配质量的一致性,并通过力觉传感器进行去毛刺和打磨, 以提升铸件的产品质量和外观。在电子电气行业,FANUC 机器人的高速度和高精度使 其非常适合电子元件的装配,包括 SMT 贴装和电路板组装。它们内置的视觉系统不仅 能够进行元件的精确放置,还能进行质量检测,从而提高电子产品的可靠性。此外, FANUC 焊接机器人在执行精密焊接作业时,保证了焊缝的质量和一致性。而在食品饮 料行业中,FANUC 机器人在包装线上自动化包装,提升包装速度和准确性,同时利用 视觉系统对食品进行外观和质量检测,确保不合格产品被有效剔除。在重物搬运和码垛 工作中,尤其是在饮料箱的堆叠和仓库搬运中,FANUC 机器人展现出卓越的性能。这 些应用展示了 FANUC 机器人在不同行业中的广泛适用性和高效性,为自动化生产提供 了强有力的支持。FANUC 的工业机器人通过其高可靠性、高生产效率和高通用性的特 点,能够为上述行业提供定制化的自动化解决方案,帮助企业提高生产效率、降低成本、 提升产品质量,并增强市场竞争。
(四)产品结构端:看战略转型方向(出海&产品上下游拓宽)
面对单一业务周期性波动,上下游拓宽产品矩阵对冲风险。发那科的工业机器人业务从 2011年的 1148亿日元增长至 2023年的 3809亿日元,逐渐成为公司的支柱性业务。面对 公司 FA 和数控机床业务的周期性波动,公司平衡拓宽业务,对冲了经济周期带来的风 险。尤其是 2010 年以后,以中国为代表的新兴经济体产业自动化升级进一步加速,发 那科工业机器人销量再度放量增长,收入占比逐渐提升。2023 年发那科工业机器人、 FA、数控机床业务占比分别达到 48%、23%和 13%。
面对日本需求低迷,海外市场是发那科长期增长的核心动力。作为全球领先的自动化企 业,发那科如果仅依赖日本市场,发展潜力将受到限制,因为数控技术和工业机器人在 日本的市场密度最终会达到饱和点。从上世纪 80 年代后期开始,日本经济面临一系列 挑战,包括日元升值、泡沫经济破裂和人口老龄化,导致国内经济陷入低迷。在这种背 景下,以中国和韩国为代表的新兴工业化国家,为发那科开辟了新的增长渠道。2016 到 2023 年,发那科的海外收入占比一直保持在 75%以上的高位,到 2023 年,发那科的海 外收入达到了 6902 亿日元,占比高达 87%。
深耕海外市场,全球化布局日渐成熟。自成立以来,发那科始终积极开拓海外市场。 1976 年与西门子在美国合资成立 GENERAL NUMERIC CORPORATION,1977 年 FANUC USA CORPORATION 成立,1978 年 FANUC EUROPE SA 成立,1982 年与通用 汽车合资成立 GM-Fanuc 机器人公司,1986 年与 GE 公司合资成立 GE-Fanuc 自动化公司 并于 90 年代后,大举进军中国、印度等新兴经济体,掌握发展中国家“智造”升级的 先发优势。2023 年发那科在中国大陆、其他亚洲地区、美洲、欧洲的占比分别达到 21.6%、14.2%、28.6%、21.2%。
发那科建立了覆盖全球的销售和服务网络。发那科的研发实验室主要集中在日本,所有 核心产品也在日本的工厂进行加工。尽管本土化生产无法享受发展中国家低成本劳动力 的优势,但发那科的工厂自动化和智能化程度极高,实现了用机器人制造机器人的生产 模式,使得本土生产仍然具有显著的竞争力。在强大的本土研发和生产技术支持下,发 那科在全球范围内建立了广泛的销售和服务网络,覆盖了 106 个国家,并设立了 282 个 服务网点。只要客户使用发那科的产品,公司将始终提供维修和零件更换服务。这种全 面的服务体系不仅提升了客户满意度,也增强了发那科在全球市场的竞争力。
三、内外之论:当国内工业机器人市场增速放缓
(一)我国制造业面临的困境:劳动力市场的转变和产业升级的需求
我国的劳动力总量面临下行压力。随着人口老龄化的加剧和生育率的下降,适龄劳动人 口的数量正在减少。根据国家统计局公开数据显示,2013 年至 2023 年,我国劳动年龄 人口下降超 4800 万人,劳动年龄人口占比在 2012 年达到顶峰,随后逐年下降。据国务 院发展研究中心《未来十年我国劳动力供求趋势分析》报告预测,从 2020 年至 2030 年, 我国适龄劳动人口规模将从 9.89 亿人下降到 9.63 亿人。劳动参与率也预计将从 68.44% 下降到 65.17%,导致劳动力供给规模持续下降;到 2030 年,劳动力供给总量预计将降 至 6.27 亿人左右。
我国社会老龄化程度不断加重。抚养比是指非劳动年龄人口(通常是 14 岁以下和 65 岁 以上的人口)与劳动年龄人口(15-64 岁)的比例。随着老龄化的加速和生育率的降低, 我国的总抚养比呈上升趋势。这意味着越来越少的劳动年龄人口需要支持越来越多的非 劳动年龄人口,这对劳动力市场和社会保障体系带来了较大的压力。分解总抚养比的变 化发现,相较于总体的上升趋势,少年儿童的抚养比呈现反向的下降,而老年人口上升 迅速,间接验证了人口老龄化、后备劳动力不足的状况。根据 OCED 预测,我国人口抚 养比将会在 2030 年、2060 年分别达到 0.63 和 0.95,这意味着每个劳动年龄人口需要平 均抚养 0.63 或 0.95 个非劳动年龄人口。
农民工是一线制造业的重要力量,整体老龄化程度加剧。农民工一直是我国制造业劳动 力的重要来源,早期进入城市的农民工,随着年龄的增长,逐渐进入了老年阶段;这部 分人口由于年龄、健康和技能等因素,逐渐退出了劳动力市场,导致农民工整体数量的 减少;据国家统计局数据,我国农民工中制造业从业占比从2008年的37.2%下降至2023 年的 27.5%;五十岁以上人口比例也从 2008 年的 11.4%增长至 2023 年的 30.6%。与上一 代农民工相比,新生代农民工的教育水平普遍较高,对于工作的选择更加多样化,不再 局限于传统的制造业和建筑业等劳动密集型行业。这导致他们更倾向于选择有更好发展 前景和工作环境的岗位,从而减少了传统制造业中的农民工数量。随着经济的发展和产 业结构的升级,对劳动力的技能要求也在不断提高。一些年龄较大的农民工可能缺乏适 应新岗位所需的技能和知识,因此在就业市场上的竞争力下降,进而影响他们的就业机 会和数量。
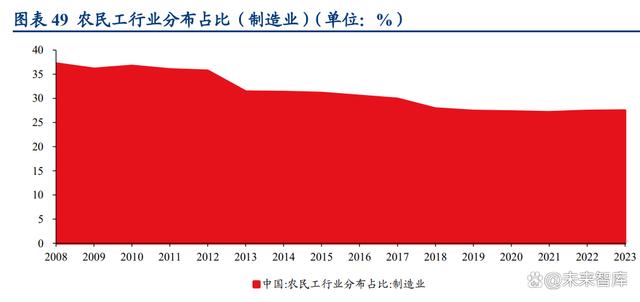
我国农民工人口流动趋势减缓。随着中西部地区经济的发展和产业转移,一些农民工选 择在家乡或就近地区就业,减少了跨省流动的需求。随着社会的进步和生活水平的提高, 农民工对于家庭和生活质量的考虑也在增加。一些农民工为了子女教育、家庭团聚等生 活因素,选择留在家乡或就近就业,减少了外出务工的人数。除此之外,疫情也对于人 口流动产生了一定的影响。国家统计局相关数据显示,我国外出农民工人数增长速度逐 渐放缓,这与制造业对于劳动力的需求并不匹配。
我国劳动力市场供求关系促使制造业从业人员薪资上涨。根据国家统计局数据,自 2009 年以来,我国制造业农民工的收入逐年攀升,到 2023 年已达到 4780 元。经过测算 发现,随着我国劳动力成本持续上涨,部分发达地区制造业用工成本或已高于工业机器 人成本。根据赛辉集团招股书援引欧睿 passport 数据库,我国制造业员工时薪从 2018 年 至 2022 年按 7.5%的复合年增长率稳步增长,于 2022 年达到 5.6 美元(约 40 元),预计 于 2027 年继续增至 7.4 美元。劳动力成本的提升促使企业寻求人力的替代品,从而催生 了“机器替人”的趋势。
我们测算,我国工业机器人每小时成本在 15 元左右,低于制造业员工时薪。我们参考 目前市场上较有代表性的 20kg 六自由度通用类关节工业机器人,本体价格在 10 万左右 (综合考虑进口与国产品牌差异),并做出如下假设: 1)集成费用约是工业机器人本体费用1倍左右(包括安全栅栏、引进安全PLC、工具、 集成时间、编程培训或招募工业机器人程序员评估等); 2)一般售后集成商会陪产 1 年左右主要进行工业机器人调试培训等工作,费用约为工 业机器人成本 10%; 3)工业机器人维护升级工作由工业机器人本体制造商负责,前期较低,后期较高,维 护费用在工业机器人成本的 2%-5%。
考虑到终端客户对成本回收期及产品升级对实际使用寿命的影响,假设更换周期为 5 年, 测算出工业机器人的单位小时成本为 15.10 元。
(二)全球市场周期性显著,我国成为中坚力量
全球工业机器人销量持续增长。根据 IFR 数据,2022 年全球工业机器人销量连续第二年 突破 50 万台,同比增长 5%;预计到 2024 年全球机器人销量将达到 62.2 万台。随着新 一轮科技革命和产业变革蓬勃兴起,人工智能、传感等新一代数字技术与机器人产业加 快融合,推动了机器人产业技术创新的步伐,使原有应用领域的机器人性能更强,也开 拓了新的应用领域。全球工业机器人的需求市场主要集中在制造业规模大、自动化水平 相对较高的国家,目前全球 70%以上的工业机器人部署在中国、日本、美国、韩国和德 国,2022 年这五大市场工业机器人销量占全球的79.1%。
我国是全球最大的工业机器人市场,传统行业占比提升。据 IFR,我国连续多年成为全 球最大工业机器人市场,全球出货量占比由 2012 年的 14%提升至 2022 年的 52%,占据 一半以上市场份额。从行业结构看,全球工业机器人的需求半数以上来自汽车行业和电 气电子行业。此外,工业机器人也大量应用于食品、医药等行业的生产线上,通过提高 生产效率和准确性,帮助企业降低成本、提升竞争力。在数字技术进步的推动下,机器 人供应商和系统集成商提供新的应用程序并改进现有应用程序的速度和质量,机器人正 在改变制造业,将越来越多地作为互联数字生态系统的一部分运行。
工业机器人全球化程度加深,国际周期保持相对一致性。各国在工业机器人领域的技术 交流和市场融合不断加强,使得全球市场的供需动态和发展趋势愈发同步。据 IFR,美 国、日本的工业机器人销量由2012年的2.2万、2.9万台增长至2022年的4.0、5.0万台, 整体增速变化与全球工业机器人销量增速的变化具有较高一致性。这种一致性有助于全 球产业链的协调和稳定,推动技术进步与产业升级。与此同时,全球市场的紧密联系也 使得单个市场的波动更易传导至其他地区,强化了全球工业机器人市场的联动性。
(三)我国:工业机器人“十年十倍”增长,下一阶段聚焦“出海”
我国工业机器人行业成长性显著。从整体销量来看,工业机器人 “十年十倍”增长, 由 2012 年 2.7 万台提升至 2022 年 28.2 万台,在产业升级机器替人大背景下,伴随着制 造业景气度周期波动,整体呈现螺旋式增长态势。历年周期大致分为四个阶段: 1)产业化初期:市场体量较小,本土机器人公司较少,以海外品牌在汽车产线应用为 主。 2)百花齐放期:受益于政策扶持和传统产业转型升级的拉动,大批量国内公司进入工 业机器人赛道,产业链初步形成。 3)大浪淘沙期:一方面新兴产业拉动工业机器人需求,另一方面中低端市场激烈的价格竞争加速第一轮洗牌。 4)进口替代期:零部件自主化程度提升、汽车产业链国产化、焊接等高端需求释放加 速国产头部品牌进口替代。
得益于核心零部件国产化及机器人控制器技术能力提升,国产一线品牌从两头受气到上 下突围。一方面,RV 及谐波减速器实现国产化有利于国产一线整机进一步通过技术优 势抢占中低端应用,向下突围价格差异不大而性能优势突出;另一方面,机器人控制器 及驱动技术的提升进一步缩小了与外资品牌的产品力差距,向上突围性能差异不大而价 格优势突出,从而实现“上顶下沉”。据睿工业,本土品牌市占率由 2021 年的 32.1%提升至2023 年的 45.1%,创历史新高。国产品牌已形成相对完整的工业机器人产业链,产 品质量、核心技术自主能力、品牌知名度也在不断提升,预计 2024 年市场份额将进一 步扩大,国产替代加速进行。
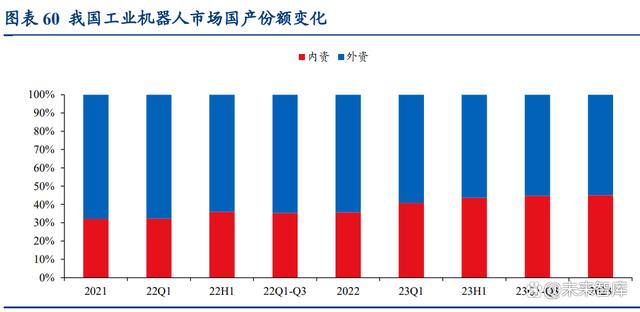
我国工业机器人“去库存”已进入尾声,核心关注点在于市场需求复苏。据 MIR 睿工 业,2023 年下半年,我国工业机器人厂商通过产品促销、拓展并加大渠道激励等措施来 清库存;到 2023 年底,市场“去库存”已进入尾声,预计 2024 年市场进入低库存周期, 核心关注点在于市场需求复苏。2023 年我国工业机器人下游行业中,光伏增速最高,主 要系各工艺环节渗透率均持续提升,如硅片清洗、包护角、接线盒安装、装/卸工装夹 具等,内资机器人企业紧抓光伏全产业链机会,销量快速增长,外资则聚焦电池片环节 提供高附加值方案;电子、锂电、金属制品等行业需求持续萎缩。
国内市场需求放缓,海外市场开拓势在必行。据 IFR,我国工业机器人的进口均价整体 处于波动下降趋势,体现国产工业机器人认可度提升过程中外资品牌溢价能力的下降。 同时,我国工业机器人市场存在一定的供需“剪刀差”,供给的饱和进一步加剧市场竞 争,进行海外市场拓展逐渐成为行业提升天花板的重要手段,越来越多国产机器人品牌 将目光投向日韩、东南亚、欧美等国际市场以寻求新的增长点。
四、重点公司分析
(一)汇川技术:国内工业自动化龙头,打造机器人一体化服务
汇川技术的工业机器人产品涵盖机器人系统、机器人控制柜、机器人软件以及各种机器 人选配件,基本完全覆盖客户的业务需求,做到一体化服务。公司的 SCARA 机器人系 列适应多场景应用需求,从 IR-S4 到 IR-S50,以及 IRS111-3 等产品,可广泛灵活运用于 3C、锂电、光伏、显示、汽车零部件、搬运、机械组装等场合;六关节机器人系列则主 要针对精密智能制造,产品主要特点在于结构紧凑,柔性化高,精度高。除此之外,汇 川技术还推出了 IR-C8 系列产品作为定制机器人方面的主力产品,主要针对客户极致产 线设计需求。并且,客户能在挑选机器人产品的基础上选配机器人控制柜以及各种配套 设备及零件,充分做到覆盖需求广泛,产品结构立体多样。
汇川的通用自动化业务和 SCARA 机器人应用市场可以实现高度重合。2023 年汇川 SCARA 机器人产品销量在中国市场的份额约 20.8%,位居第一名。伴随着汇川通用自 动化市场渗透率不断提升,其忠于客户价值的服务体系使得自身累积了不同行业、不同 规模、不同发展阶段企业的应用实例,使之能够快速精准洞悉客户的痛点,与客户共创。 这些对各个行业的工艺梳理和大客户的储备都是汇川 SCARA 机器人市场开拓的重要筹 码。汇川庞大的客户资源池以及丰富的行业经验,以及大型客户的品牌信任度,是其他 国产品牌短期难以拥有的资本。
(二)埃斯顿:2023 年工业机器人出货量位居国产品牌第一,核心零部件自主率高
埃斯顿在工业机器人及智能制造系统领域有着广泛的布局,提供全系列工业机器人和运 动控制系统解决方案。主要产品涵盖工业机器人、自动化核心部件及运动控制系统两大 部分。埃斯顿的全系列工业机器人覆盖 3-700KG 负载,共有 87 款工业机器人。类型上 包括 SCARA、桌面 MINI、专用型及多关节机器人。埃斯顿一直坚持独立正向的研发战 略,区别于传统研发平台,将一切技术建立在客户需求基础上,即由客户需求转化为产 品需求,进一步转化为技术方案,率先实现了机器人控制器、伺服系统、本体设计的全 方位布局,机器人核心零部件自主率达到 95%以上。
凭借全产业链优势,为各行各业打造成熟的自动化系统完整解决方案。针对锂电、光伏、 汽车、装备机械、家具建材等行业工艺需求,埃斯顿拥有 220~700kg的 10款重负载机器 人,满足各类复杂场景应用。针对精度、运动性能和安全控制能力的高要求,埃斯顿重 负载机器人拥有 4 大核心技术优势,分别是多目标系统优化技术、误差估算与补偿算法、 高负载下最优运动最优轨迹规划及高精度运动控制、高速度振动抑制技术,满足客户精确高效的制造需求。
(三)埃夫特:加强焊接、喷涂和通用平台产品,提升国外影响力
埃夫特目前有多个工业机器人产品系列,主要产品型号包含 ESR 系列、ARC 系列以及 ER 系列,从应用类型上看包括了协作机器人、焊接机器人、喷涂机器人以及码垛机器 人。公司产品覆盖了多种应用场景,从轻型搬运到重型加工,具有不同的负载能力和工 作范围。具体特点包括高精度、高速度、多轴控制以及多种接口,适用于汽车、电子、 食品、医疗等多个行业。通过提供多样化的产品线,公司构建产品与解决方案方面注重 细化产品的功能应用,具体到分类产品的组装、涂胶、焊接、喷涂、搬运、打磨等功能。
以机器人产品为纽带,进一步强化境内外业务的协同。公司开始以意大利子公司为埃夫 特机器人在欧洲的抓手,建设埃夫特机器人在欧洲的销售网络、技术支持体系和售后服 务体系,参加法国国际工业展 Global Industrie 2023 以及意大利国际工业展览会 MecSpe2023,打响埃夫特机器人品牌在欧洲的知名度,完善埃夫特机器人在欧洲的战 略合作伙伴销售网络,落地了一些细分行业的示范应用和推广应用,提升埃夫特机器人 在欧洲的可见度,提升埃夫机器人品牌在国外的影响力。
(本文仅供参考,不代表我们的任何投资建议。如需使用相关信息,请参阅报告原文。)
精选报告来源:【未来智库】。